Quando Jeep stava allestendo lo stabilimento per produrre il suo nuovo SUV, in uno degli impianti produttivi automobilistici più moderni nello Stato di Pernambuco, le condizioni erano chiare e dirette. Comau sarebbe stata responsabile dell’ampliamento dei sistemi di assemblaggio della carrozzeria per permettere alla casa automobilistica di produrre il nuovo SUV a 7 posti Jeep Commander tramite un metodo di produzione flessibile, interamente alternato con altri 3 modelli già in produzione, garantendo la stessa capacità produttiva di 48 veicoli all’ora, eventualmente ampliabile in futuro. Per aumentare il parco industriale, Comau ha aggiunto 24 nuovi robot, 24 pinze di saldatura e 4 nastri trasportatori agli oltre 620 robot di assemblaggio e saldatura già installati nella fabbrica automobilistica Jeep di Goiana. Inoltre, gli interventi nelle 14 linee di produzione progettate da Comau, che combinavano operazioni automatiche, semi-automatiche e manuali, sono stati eseguiti durante il naturale periodo di inattività dell’impianto per garantire il minimo impatto sulla produzione.
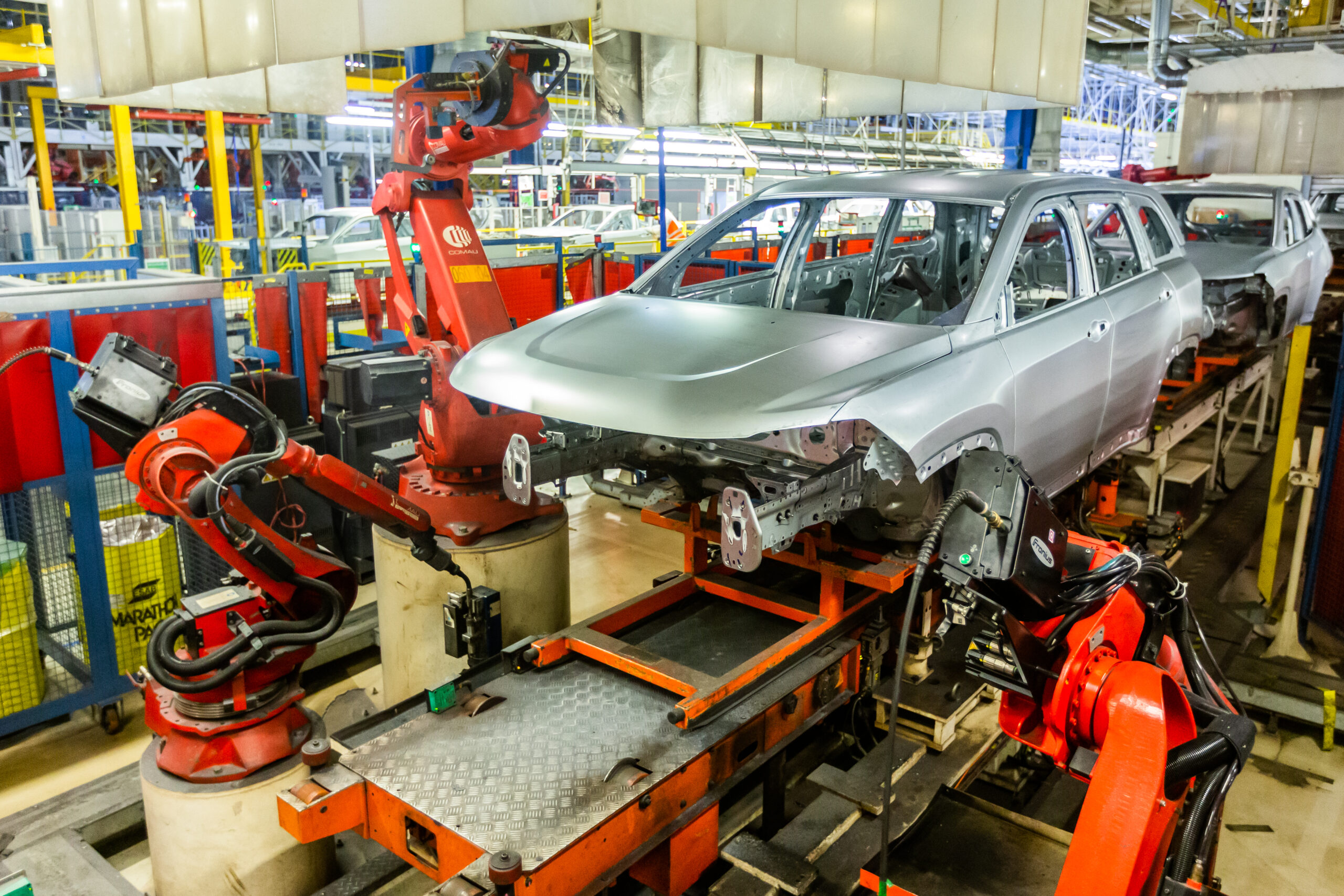

“Sin dall’inizio del progetto, Comau ha dimostrato la propria competenza tecnica, esperienza nel campo dell’automazione e impegno verso il nostro successo”, racconta Mateus Marchioro, manager dell’impianto Jeep. “Nonostante il fermo dello stabilimento di almeno 2 mesi dovuto alla pandemia di COVID-19, il team è stato in grado di portare a termine tutte le fasi del progetto in anticipo sulla tabella di marcia. Ma soprattutto, le soluzioni proposte richiedevano meno apparecchiature ausiliarie e meno elaborazione manuale rispetto a quanto previsto inizialmente. Siamo soddisfatti del risultato generale delle nuove linee.”
Mateus Marchioro, manager dell’impianto Jeep
La sfida
La sfida lanciata da Jeep a Comau era quella di progettare una soluzione innovativa che avrebbe permesso alla casa automobilistica di produrre il suo nuovo SUV sulle stesse linee di produzione che già producevano 3 dei veicoli più venduti in Brasile, senza sacrificare gli obiettivi di produzione o i tempi di ciclo. Migliorare il livello di automazione e migliorare l’efficienza del processo era un’ulteriore sfida, perché i cambi di strumentazione necessari per passare da un modello all’altro avrebbero generato inefficienze se non studiati attentamente. Infine, le linee avrebbero dovuto avere la flessibilità intrinseca necessaria per permettere a Jeep di introdurre nuovi modelli in futuro.
Il know-how tecnico di Comau e la completa integrazione con il team di ingegneri Jeep hanno garantito alla casa automobilistica un progetto ben eseguito e completato nei tempi previsti. Dopo aver mappato i cicli di produzione reali, gli ingegneri di Comau hanno lavorato con strumenti di simulazione per ottenere un quadro più completo delle modifiche proposte al layout della linea di assemblaggio prima di qualsiasi implementazione. La diagnosi precisa di dove e come venivano utilizzate le attrezzature e le risorse ha garantito che tutte le modifiche fossero rappresentate in uno scenario virtuale, indipendentemente dalla loro origine. Questo ha permesso al team di ottimizzare la messa in servizio nell’impianto e di ridurre al minimo i tempi di inattività legati all’implementazione. Il team si è anche avvalso della messa in servizio virtuale per programmare la simulazione dei processi e accelerare l’implementazione delle linee.
La soluzione
Per soddisfare le esigenze di Jeep per quanto concerneva la flessibilità dei modelli, gli ingegneri di Comau hanno dovuto espandere la capacità dell’innovativo sistema Butterfly da 3 modelli a 4 modelli, con un ordine di produzione casuale. Il sistema, progettato sostanzialmente per pianificare lo spazio fisico delle nuove attrezzature e dei robot quando vengono introdotti nuovi modelli, avrebbe dovuto per la prima volta gestire 4 modelli. In un punto della linea, 14 robot applicano 100 punti di saldatura in 52 secondi per unire contemporaneamente le fiancate e il telaio in un’unica operazione, assicurando una geometria perfetta alla carrozzeria. In un’altra fase, 70 robot applicano l’adesivo strutturale per fornire maggiore rigidità e resistenza alle infiltrazioni di polvere e acqua. In tutto, ogni veicolo riceve più di 3.000 punti di saldatura durante il processo di assemblaggio.
Altre modifiche alla linea includono il miglioramento del sistema automatico di saldatura e assemblaggio di Comau, VersaRoll. Così facendo, il team di ingegneri ha eliminato la necessità di calibrare il dispositivo ottimizzando il numero di robot per stazione. Similmente, il Tool Tray Shuttle è stato ampliato per operare su 4 tavoli per la prima volta e per adattarsi meglio alle specifiche esigenze di assemblaggio del nuovo SUV.
Per affrontare le sfide legate alla pandemia, che includevano l’impossibilità di accedere all’impianto durante il periodo di chiusura forzata, Comau do Brasil ha adottato un approccio fluido alla gestione del progetto. Il team ha lavorato in smart working, sfruttando progetti di simulazione delle celle e strumenti di messa in servizio virtuale prima di passare ad un ritorno graduale e sicuro alle attività all’interno dello stabilimento. Il team ha anche dovuto gestire i ritardi nella consegna dei componenti ed è stato in grado di farlo concentrandosi sulle parti del progetto per le quali le forniture erano disponibili in tempo. Comau è così riuscita ad anticipare la tabella di marcia, realizzando il Progetto 598 in meno di 24 mesi dall’inizio alla fine. E soprattutto questo è stato realizzato senza compromettere il flusso o i volumi naturali di produzione dell’impianto Jeep di Goiana.
I risultati
Grazie all’approccio del lean manufacturing, la soluzione innovativa di Comau registra un’alta percentuale di processi di automazione avanzata e coinvolge meno apparecchiature ausiliarie. Invece di sensori e fotocellule, si usano telecamere per rilevare i pezzi in base alla forma. La completa digitalizzazione 3D delle stazioni della linea ha garantito un perfetto allineamento robotico. Sono state implementate anche soluzioni proprietarie di Comau, come la saldatura laser, la visualizzazione e i sistemi di ritaglio Roller Hemming – RHEvo. Oltre a questo, la configurazione compatibile con l’Industria 4.0 utilizza la tecnologia IO-link per aiutare a monitorare processi importanti, come gli impianti dell’acqua e dell’aria compressa e aiuta a rilevare eventuali problemi in modo molto rapido ed efficace. Tutto questo offre a Jeep un’alta efficienza delle attrezzature e il miglioramento delle risorse di controllo della qualità.
Per aiutare a proteggere la scalabilità degli investimenti del cliente, l’intero progetto è stato sviluppato per permettere a Jeep di introdurre nuovi modelli in futuro. Inoltre, il progetto portato avanti in Brasile rappresenta la capacità globale di Comau di rispondere a sfide complesse con i più elevati standard di fabbricazione, grazie alla collaborazione diretta dei professionisti di Comau Romania, Comau Italia e Comau Cina. Comau do Brasil ha così potuto sfruttare la sua presenza locale e la sua esperienza di lunga data nell’automazione, nella digitalizzazione e nelle tecnologie intelligenti per fornire velocità, qualità ed efficienza su cui Jeep potrà contare per produrre i suoi veicoli premium.
modelli di veicoli assemblati in un complesso di 14 linee con ordine di produzione casuale
+
robot Comau installati
punti di saldatura applicati ogni 52 secondi
perdite di produttività durante il processo di espansione